The field of electronics 3D printing is among the most exciting for the industry as a whole, as developments in the space could lead to further developments in the 3D printing of whole, functional objects, rather than individual components. Research at the University of Southampton, then, could push progress in this direction, as the school’s researchers explore the 3D printing of optical fibers.
In order to manufacture optic fibers, what is called a preform is first made, seeing the material of choice, often silica or germania, formed inside of a tube. The material is then drawn out in long strings to create fine fiber optic cables. Unlike previous methods of producing optical fiber, which limit its shape and make-up, the Southampton team is hoping to 3D print the stuff in order to create uniquely shaped optical fiber objects. The technology is being created by Professor Jayanta Sahu, of the University of Southampton’s Zepler Institute, and Dr. Shoufeng Yang, the Faculty of Engineering and Environment, and relies on Multiple Materials Additive Manufacturing. Prof. Sahu explains, “We will design, fabricate and employ novel Multiple Materials Additive Manufacturing (MMAM) equipment to enable us to make optical fibre preforms (both in conventional and microstructured fibre geometries) in silica and other host glass materials. Our proposed process can be utilised to produce complex preforms, which are otherwise too difficult, too time-consuming or currently impossible to be achieved by existing fabrication techniques.”
The Southampton team is attempting to get beyond the limits of the “stack and draw” technique for traditional fiber optics manufacturing, which sees thin glass rods stacked together create the preform, by 3D printing pure glass powder. This would allow the researchers to create more complex structures. Matthew Peach, at Optics.org, points out, however, some of the obstacles of such a process, “There are numerous challenges including the high melting temperature of the glass (over 2000?C in case of silica); the need for precise control of dopants, refractive index profiles and waveguide geometry; and the need for transitions between the layers to be smooth, otherwise the properties of the resultant fibre will be altered.”
The work is being funded with £700,000 ($1.1 million) from the Engineering and Physical Sciences Research Council (EPSRC) and will see industry participation from UK firms that will contribute to the development of the technology. ES Technology will be able to lend its expertise as a provider of laser material processing systems, while Fibercore is a specialty fiber supplier, and SG Controls is a manufacturer of optical fiber equipment. Together with Southampton, they may be able to create a 3D printing technology that could change a variety of industries.
Professor Sahu adds, “We hope our work will open up a route to manufacture novel fibre structures in silica and other glasses for a wide range of applications, covering telecommunications, sensing, lab-in-a-fibre, metamaterial fibre, and high-power lasers. This is something that has never been tried before and we are excited about starting this project.” Optics.org indicates that one such application would be the production of a photonic bandgap fiber (a diagram of which is above), a low-loss and wide bandwidth fiber sought after by telecommunications companies.? The fiber, which is hollow except for sub-micron scale nodes and struts, could previously not be made at very long lengths, until another group of Southampton researchers pulled it off. While Peach believes that such a fiber could be printed with Prof. Sahu’s technology, 3D printing enthusiasts know that rods are just the beginning for such a powerful manufacturing system and much more intricate shapes could be on the way.
自動翻譯僅供參考
南安普敦大學啟動了多項對3D光纖打印項目
電子3D打印領域是整個行業(yè)中最令人興奮的領域,因為空間的發(fā)展可能會導致3D打印整個功能對象而不是單個組件的進一步發(fā)展。屆時,南安普敦大學的研究將推動這一方向的進展,因為該校的研究人員正在探索光纖的3D打印。
為了制造光纖,所謂的預成型件先制成,看到所選擇的材料,常常二氧化硅或鍺,一個管的內(nèi)部形成。然后將材料拉出長串創(chuàng)建精細光纖電纜。不同于生產(chǎn)光纖以前的方法,這限制了它的形狀和化妝,南安普頓隊希望到3D以創(chuàng)造獨特形狀的光纖對象打印的東西。該技術(shù)是由Jayanta薩胡南安普敦的Zepler學院大學教授,和手縫Yang博士,工程與環(huán)境學部創(chuàng)建,并且依賴于多種材料的添加劑制造。薩胡教授解釋說,“我們將設計,制造和采用新的多材料添加劑制造(MMAM)設備,以使我們能夠在二氧化硅和其它主機玻璃材料的光纖預制棒(包括常規(guī)和微結(jié)構(gòu)光纖幾何形狀)。我們提出的方法可用于產(chǎn)生復雜的預成型件,這是否則太難,太費時或目前不可能由現(xiàn)有的制造技術(shù)來實現(xiàn)?!?/span>
南安普頓隊試圖超越傳統(tǒng)的光纖制造“棧和畫”技術(shù),它看到疊在一起創(chuàng)建預制棒薄玻璃棒,通過三維打印純玻璃粉末的限制。這將允許研究人員來創(chuàng)建更復雜的結(jié)構(gòu)。馬修桃,在Optics.org,所指出的,然而,一些這樣的方法中的障礙,“有許多挑戰(zhàn),包括玻璃的高熔解溫度(超過2000℃的情況下二氧化硅的?);需要的摻雜劑,折射率分布和波導幾何形狀精確控制;并且需要在層之間的過渡是光滑的,否則所得到的纖維的性質(zhì)將被改變?!?/p>
這項工作正在資助與工程和物理科學研究理事會(EPSRC)£70萬($ 110萬美元),將看到英國公司,這將有助于該技術(shù)的開發(fā)行業(yè)的參與。 ES技術(shù)將能夠提供其專業(yè)知識,激光材料加工系統(tǒng)供應商,而Fibercore公司是一家特種纖維供應商和SG控制的光纖設備制造商。連同南安普敦,它們可能能夠創(chuàng)建3D印刷技術(shù),可以改變各種行業(yè)。
薩胡教授補充說:“我們希望我們的工作將開辟一條途徑來制造新的纖維結(jié)構(gòu)二氧化硅和其他玻璃的應用范圍廣泛,涵蓋了通訊,傳感,實驗室-IN-A-纖維,超材料纖維,和高功率的激光器。這是一件以前從來沒有嘗試過,我們很興奮開始這個項目。“Optics.org表明一個這樣的應用將是生產(chǎn)光子帶隙光纖(圖這是以上),低損耗和寬帶光纖電信公司追捧?的纖維,它是空心除了亞微米級的節(jié)點和支柱,可預先不能在很長的長度制成,直到另一組南安普敦研究者把它關閉。雖然桃認為,這種纖維可以印有薩胡教授的技術(shù),3D打印愛好者知道棒僅僅是個開始為這樣一個強大的制造體系和更復雜的形狀可能是在路上。
-
3D打印
+關注
關注
27文章
3589瀏覽量
112409
發(fā)布評論請先 登錄
答疑|3D打印能打印立體字母嗎?
3D打印技術(shù):如何讓古老文物重獲新生?
3D打印中XPR技術(shù)對于打印效果的影響?
高分子微納米功能復合材料3D打印加工介紹
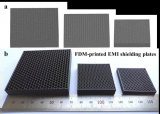
有源晶振在3D打印機應用方案
UV光固化技術(shù)在3D打印中的應用
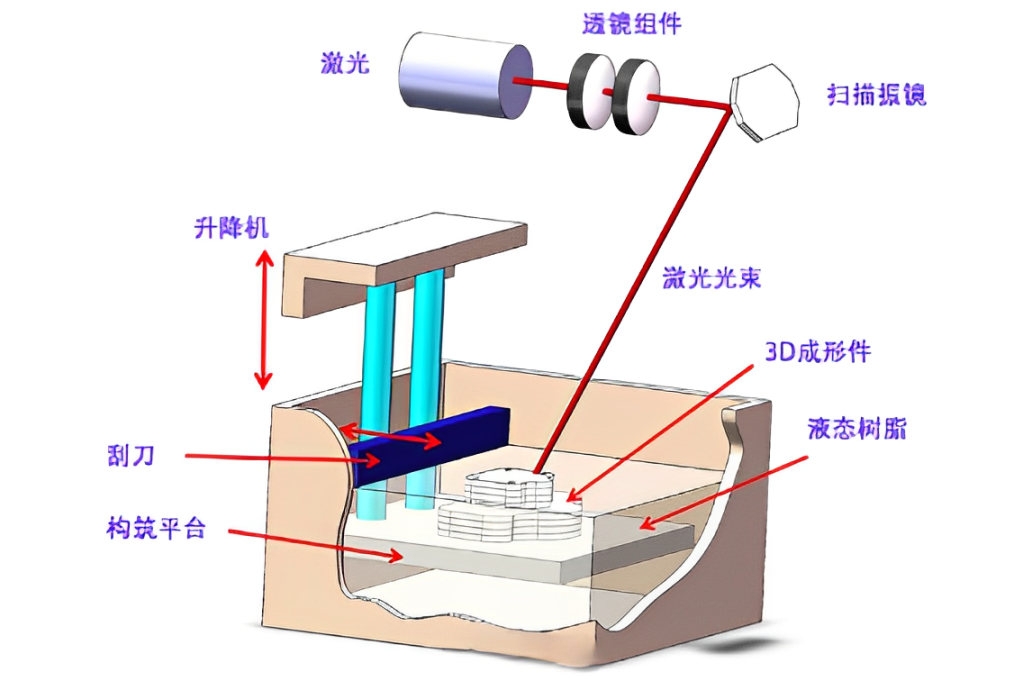
3D打印技術(shù)應用的未來
物聯(lián)網(wǎng)行業(yè)中的模具定制方案_3D打印技術(shù)分享
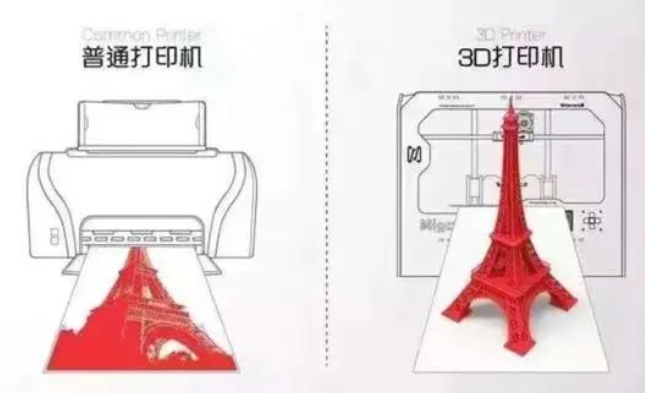
物聯(lián)網(wǎng)行業(yè)中的模具定制方案_3D打印材料選型分享
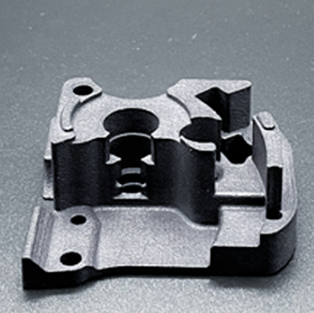
維愛普3D打印設備工字電感磁芯:驅(qū)動創(chuàng)新與高效的科技核心
3D打印汽車零部件建模設計3D打印服務
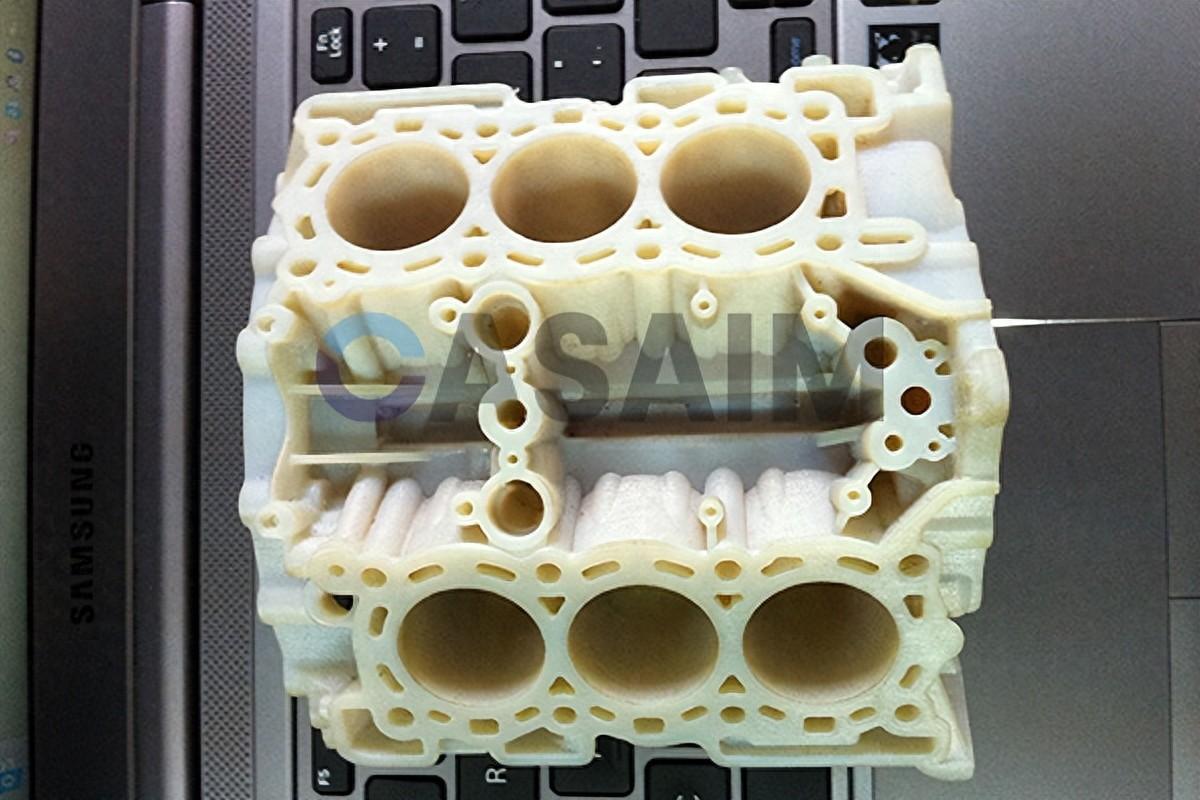
評論