(文章來源:激光天地)
X射線斷層掃描技術(shù)作為一種具有獨(dú)特的功能的無損檢測技術(shù),可以用來分析增材制造(AM)產(chǎn)品的缺陷。缺陷的類型包括氣孔、表面粗糙不平、尺寸偏差等。其形成的原因由于樣品的不同而有較大的差異。粉末性能、輸送粉末時(shí)不均勻、制造過程中的變形、激光束變化時(shí)造成的工藝參數(shù)的偏離、光學(xué)部件和掃描系統(tǒng)的操作等均會造成未熔合氣孔、冶金氣孔、匙孔效應(yīng)氣孔的生成。這些不同類型的氣孔具有不同的類型尺寸、形狀和3D空間分布,所有類型的缺陷均會對最終產(chǎn)品的機(jī)械性能造成影響。采用X射線斷層掃描技術(shù)在零件進(jìn)行機(jī)械性能測試前進(jìn)行無損觀察,可以有助于我們更好地理解氣孔缺陷對部件機(jī)械性能的影響(也稱之為缺陷的影響)。這些可以為我們提前辨別出有危害的部件提供了可能。由此為我們使用AM產(chǎn)品建立了更大的信心。本文則綜述了當(dāng)前AM技術(shù)對缺陷的影響,并對最近的相關(guān)工作做了總結(jié)。
增材制造技術(shù),尤其是鋪粉激光增材制造(LPBF),是一種發(fā)展非常迅速的制造技術(shù),可以獲得性能優(yōu)異的制品、可以制造出的材料的種類比較廣泛,尤其是可以制造形狀復(fù)雜的零件和可以進(jìn)行優(yōu)化設(shè)計(jì)是其最大優(yōu)點(diǎn),是當(dāng)今其他制造技術(shù)不能或不易實(shí)現(xiàn)的。AM技術(shù)在當(dāng)今發(fā)展迅速和取得的應(yīng)用成就為LPBF的應(yīng)用打開了廣闊的市場。由于AM技術(shù)更好的被人們所理解,其應(yīng)用則在更多的工業(yè)場景中更好的得到了應(yīng)用。個(gè)性化定制的人體植入骨如今就得到普遍應(yīng)用。
航空航天和汽車工業(yè)中對LPBF的應(yīng)用也非常感興趣。打印時(shí)較高的分辨率且可直接制造的優(yōu)點(diǎn)在牙科和珠寶工業(yè)中也得到了應(yīng)用。而且,不同的工業(yè)部件、工具和傳感器等均屬于應(yīng)用案例。LPBF尤其適合于原位合金化材料、金屬基復(fù)合材料以及個(gè)性化定制的產(chǎn)品等。AM技術(shù)或3D打印屬于同一范疇,只是不同的叫法而已。作為一種全新的制造技術(shù),可以實(shí)現(xiàn)目標(biāo)產(chǎn)品的自由設(shè)計(jì)和制造,其機(jī)械性能、疲勞性能、聲學(xué)性能,甚至于生物學(xué)性能還可以實(shí)現(xiàn)定制。AM技術(shù)還可以實(shí)現(xiàn)自我變形,即依據(jù)外部環(huán)境的變化而做出相應(yīng)地改變,這就是人們常說的4D打印。
制造過程中缺陷的存在對制品的機(jī)械性能造成了不利的影響,不管是采用何種制造技術(shù)(不光AM技術(shù)制造是如此,其他制造技術(shù)也存在)得到的制品均是如此。因此,非常有必要不斷的改善工藝和降低缺陷的不利影響。隨著X射線斷層掃描技術(shù)應(yīng)用于部件缺陷的檢測,使得依據(jù)部件缺陷尺寸或位置來檢查和判斷是否合格成為可能。這一技術(shù)應(yīng)用于鑄造件和焊接件的檢查已經(jīng)成為常規(guī)工藝。X射線斷層掃描技術(shù)已經(jīng)在材料科學(xué)、度量衡領(lǐng)域和增材制造領(lǐng)域得到應(yīng)用。采用X射線斷層掃描技術(shù)進(jìn)行AM制造的分析所花的時(shí)間和效益成本是非常有優(yōu)勢的。顯而易見,CT技術(shù)可以快速的對大體積的部件進(jìn)行掃描,同需要進(jìn)行破壞性測試和耗時(shí)較長的金相制造,然后采用金相、掃描電鏡等手段進(jìn)行分析相比是非常有優(yōu)勢的。
隨著LPBF技術(shù)的發(fā)展和LPBF的不斷應(yīng)用,越來越明顯地看到氣孔以及氣孔的分布是一個(gè)復(fù)雜的問題。不同的工藝參數(shù)、掃描路徑和制造策略、粉末材料、制造過程中的變形或其他因素均會形成缺陷并使得得到的氣孔形狀和尺寸以及氣孔的體積分?jǐn)?shù)而有所不同。不同類型的氣孔形成的原因已經(jīng)有較多的文獻(xiàn)給予了報(bào)道。同時(shí)不同類型的缺陷對制品的機(jī)械性能的影響目前并沒能完全掌握。例如,可以預(yù)見不規(guī)則的未熔合氣孔同尺寸較小的冶金氣孔或氣體逸出造成的氣孔相比,更易成為應(yīng)力集中的集中源。但對于這一說法并沒能通過實(shí)驗(yàn)去進(jìn)一步的明確。這是因?yàn)樾陆霈F(xiàn)的X射線斷層技術(shù)用于缺陷對性能的影響研究才剛剛開始,而且直到今天,控制氣孔的分布還是一個(gè)大難題。
公開報(bào)道的金屬AM制造的產(chǎn)品的機(jī)械性能差別非常大,尤其是疲勞性能的差別就更大。在大多數(shù)的關(guān)于LPBF制品的公開報(bào)道中,多集中在顯微組織和性能之間的關(guān)系研究上以及顯微組織的各向異性上。當(dāng)然,顯微組織固然重要,但目前缺陷對性能的影響在最近也開始得到人們的廣泛關(guān)注和認(rèn)可,同時(shí)急需對其進(jìn)行詳細(xì)的研究。這是因?yàn)椴煌愋偷娜毕菰谡麄€(gè)部件中的含量、最大尺寸、位置和分布(隨機(jī)的還是有規(guī)則的分布),均取決于制造系統(tǒng)。
早期關(guān)于LPBF優(yōu)化的工藝研究指出,密度為87%(氣孔的孔隙率為13%),經(jīng)過多年的努力,現(xiàn)今可以達(dá)到大于99%的密度(孔隙率小于1%),以上數(shù)值是采用阿基米德原理法測量和采用金相、掃描電鏡以及X射線斷層技術(shù)進(jìn)行分析測量的結(jié)果。同時(shí)目前已經(jīng)可能實(shí)現(xiàn)孔隙率降低到0.002%的水平,這表明目前孔隙率的變化范圍可以從13%~0.002%之間變化。尤其可見不同的孔隙率對性能的影響會有多大。
不同時(shí)間間隔時(shí)X射線斷層掃描 Ti6Al4V合金在延伸率從3.55%到9.44%之間的變化
部件形狀復(fù)雜、粉末輸送的異常、粉末尺寸和粉末形狀的隨機(jī)分布和不均勻、掃描時(shí)粉末的飛濺等、熔池中流體的流動和熔道的不穩(wěn)定等諸多因素都會造成氣孔的形成。即使對LPBF進(jìn)行工藝參數(shù)優(yōu)化、適當(dāng)?shù)母淖儝呙韬椭圃於逊e策略等,不同的缺陷依然會發(fā)生。LPBF中的氣孔在目前來說,依然不可避免,并且可以預(yù)見,較高的孔隙率必然對機(jī)械性能產(chǎn)生非常不利的影響。
眾所周知,熱等靜壓(HIP)技術(shù)是減少氣孔和改善AM組織的一種行之有效的手段。同時(shí)HIP對改善塑形和提高疲勞強(qiáng)度也是非常有效的。然而,盡管HIP在上述領(lǐng)域非常有效,但對表面缺陷在HIP處理時(shí)會保留下來,由此會損傷AM制品的性能。研究發(fā)現(xiàn),對電子束AM制造的Ti合金進(jìn)行HIP處理時(shí),氣孔又重新生成。
X射線斷層掃描技術(shù)為研究氣孔的數(shù)量和分布的無損檢測提供了關(guān)鍵的信息。比較理想的狀況是在機(jī)械性能測試之前清楚的通過X射線斷層掃描技術(shù)來獲取缺陷的影響:可能產(chǎn)生不利影響的缺陷類型、位置和分布等。材料的機(jī)械性能的含義比較廣泛,包括彈性模量、強(qiáng)度(拉伸和屈服強(qiáng)度)、塑形、剛性、硬度等靜態(tài)和準(zhǔn)靜態(tài)性能。對動載荷來說,還包括高周、低周疲勞等。
(責(zé)任編輯:fqj)
-
X射線
+關(guān)注
關(guān)注
4文章
213瀏覽量
51941
發(fā)布評論請先 登錄
為生命護(hù)航|激光跟蹤儀檢測X射線計(jì)算機(jī)斷層掃描成像系統(tǒng)的應(yīng)用
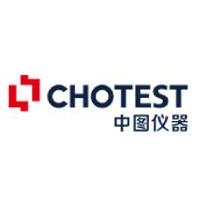
詳談X射線光刻技術(shù)
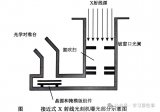
X射線應(yīng)用中的ADC前端優(yōu)化方案
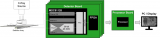
X射線熒光光譜分析技術(shù):原理與應(yīng)用
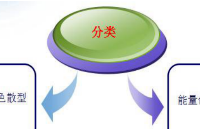
X射線掠入射聚焦反射鏡
PCBA分析儀的技術(shù)原理和應(yīng)用場景
高壓電阻器支持牙科X射線成像的準(zhǔn)確性
X-Ray射線檢測設(shè)備淺析
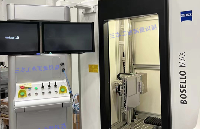
物聯(lián)網(wǎng)行業(yè)中的模具定制方案_3D打印技術(shù)分享
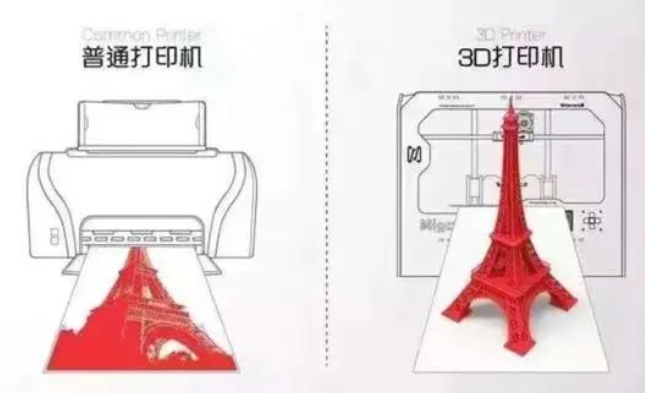
X射線工業(yè)CT檢測設(shè)備用于復(fù)合新材料內(nèi)部缺陷檢測
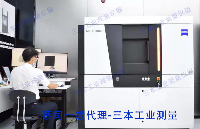
這些因素影響X-RAY射線檢測設(shè)備的價(jià)格
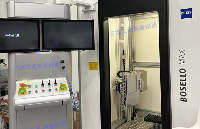
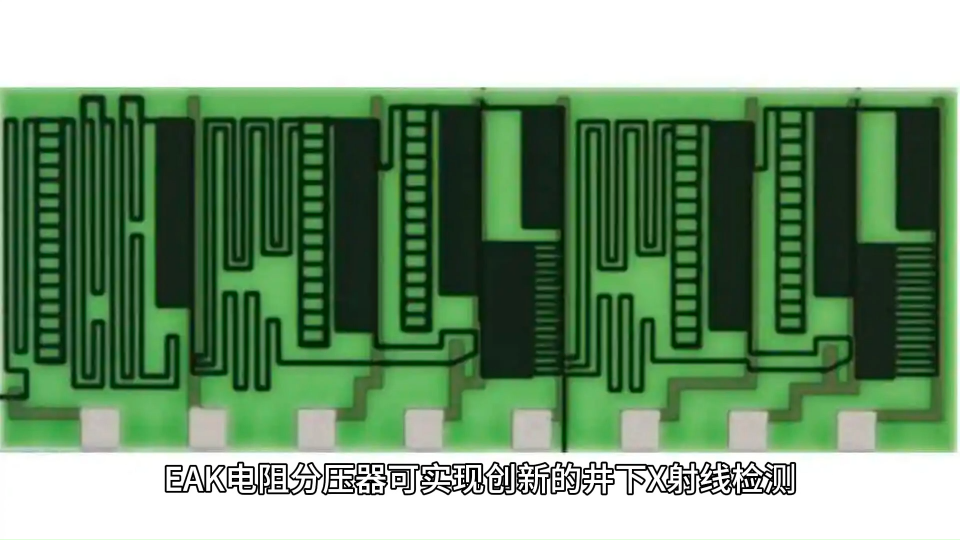
高壓功率放大器在脈沖X射線源技術(shù)及火星X射線通信中的應(yīng)用
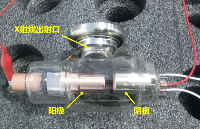
搭建光學(xué)相干斷層掃描(OCT)系統(tǒng)您需要知道
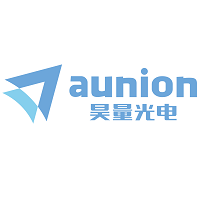
評論