芯片封裝作為半導(dǎo)體制造的核心環(huán)節(jié),承擔(dān)著物理保護(hù)、電氣互連和散熱等關(guān)鍵功能。其中,鍵合技術(shù)作為連接裸芯片與外部材料的橋梁,直接影響芯片的性能與可靠性。當(dāng)前,芯片封裝領(lǐng)域存在引線鍵合、倒裝芯片、載帶自動鍵合和混合鍵合四種主流技術(shù),它們在工藝流程、技術(shù)特點(diǎn)和應(yīng)用場景上各具優(yōu)勢。本文將深入剖析這四種鍵合方式的技術(shù)原理、發(fā)展現(xiàn)狀及未來趨勢,為產(chǎn)業(yè)界提供技術(shù)參考。
一、引言
芯片封裝是半導(dǎo)體產(chǎn)業(yè)鏈中的關(guān)鍵環(huán)節(jié),其核心目標(biāo)是將晶圓切割后的裸芯片(Die)與外部電路進(jìn)行物理連接和電氣互連,同時提供必要的機(jī)械支撐、散熱和環(huán)境保護(hù)。隨著芯片集成度的不斷提升和電子產(chǎn)品小型化趨勢的加劇,封裝技術(shù)的重要性日益凸顯。鍵合技術(shù)作為芯片封裝的核心工藝之一,直接影響芯片的電氣性能、可靠性和成本。目前,業(yè)界主流的鍵合方式包括引線鍵合(Wire Bonding)、倒裝芯片(Flip Chip)、載帶自動鍵合(TAB)和混合鍵合(Hybrid Bonding),它們各自適用于不同的應(yīng)用場景,共同推動著芯片封裝技術(shù)的演進(jìn)。
二、引線鍵合:傳統(tǒng)工藝的成熟與局限
引線鍵合是應(yīng)用最廣泛的鍵合技術(shù),其歷史可追溯至20世紀(jì)60年代。該技術(shù)通過細(xì)金屬引線(如金絲、鋁絲或銅絲)將芯片焊盤與基板焊盤連接起來,實(shí)現(xiàn)電氣互連。引線鍵合的工藝流程主要包括準(zhǔn)備、鍵合和檢測三個階段:首先,將設(shè)備預(yù)熱并裝入金屬絲;然后,通過電火花熔化金屬絲形成金球,再利用超聲波或熱壓方式將金球壓接在焊盤上形成第一焊點(diǎn);最后,通過毛細(xì)管移動形成線弧,并在基板焊盤上完成第二焊點(diǎn),切斷金屬絲后提升至指定高度,完成一個鍵合周期。
引線鍵合的優(yōu)勢在于工藝成熟度高、設(shè)備成本低、靈活性好,適合規(guī)?;a(chǎn)。然而,其局限性也十分明顯:芯片周邊的引線布置占用大量封裝空間,導(dǎo)致封裝尺寸較大;較長引線會降低電氣性能,尤其在高頻應(yīng)用中表現(xiàn)突出;引線間距的要求制約了互連密度的進(jìn)一步提升。此外,隨著芯片尺寸的縮小和引腳數(shù)的增加,引線鍵合的工藝難度和成本也在不斷上升。
三、倒裝芯片:高密度互連的突破
倒裝芯片技術(shù)(Flip Chip)起源于20世紀(jì)60年代,由IBM率先研發(fā)。該技術(shù)將芯片正面朝下,通過凸點(diǎn)(Bump)直接與基板連接,取代了傳統(tǒng)的引線鍵合方式。倒裝芯片采用區(qū)域陣列式分布的連接方式,大大提高了互連密度,縮短了信號傳輸路徑,顯著提升了封裝性能。
倒裝芯片的制作過程包括凸點(diǎn)制備、芯片組裝和底部填充三個步驟。首先,在芯片金屬接觸區(qū)域鍍上一層特殊的金屬層(UBM),再通過電鍍或其他方法形成小球狀的凸點(diǎn);然后,將芯片翻轉(zhuǎn)過來,使凸點(diǎn)正對基板上的連接點(diǎn),通過加熱使凸點(diǎn)熔化并與基板牢固連接;最后,在芯片和基板之間的空隙中注入底填膠,固化后形成保護(hù)層。
倒裝芯片的優(yōu)勢在于電氣性能優(yōu)異、散熱能力強(qiáng)、封裝尺寸小。然而,其工藝要求高,芯片翻轉(zhuǎn)對位需要精密設(shè)備和嚴(yán)格控制;芯片與基板直接相連易產(chǎn)生熱應(yīng)力問題;底填膠工藝復(fù)雜且封裝后難以返修;制造成本較高,且對芯片和基板都需要特殊的設(shè)計(jì)要求。這些因素在一定程度上限制了倒裝芯片技術(shù)的應(yīng)用范圍,但在高性能計(jì)算、移動通信等領(lǐng)域仍具有不可替代的優(yōu)勢。
四、載帶自動鍵合:高密度引線連接的自動化解決方案
載帶自動鍵合(Tape Automated Bonding,TAB)是一種將芯片組裝到柔性載帶上的封裝技術(shù)。載帶既作為芯片的支撐體,又作為芯片與外圍電路連接的引線。TAB技術(shù)的工藝流程包括載帶制作、芯片鍵合和封裝保護(hù)三個階段:首先,將銅箔貼合在聚酰亞胺膠帶上,通過光刻和蝕刻形成精細(xì)的導(dǎo)電圖形;然后,將預(yù)先形成焊點(diǎn)的芯片精確定位后,采用熱壓或熱超聲方式將內(nèi)引線與芯片焊盤連接;接著,將TAB件與基板對準(zhǔn),通過熱壓方式實(shí)現(xiàn)批量鍵合;最后,在芯片區(qū)域進(jìn)行點(diǎn)膠或模塑保護(hù),固化形成保護(hù)層。
TAB技術(shù)的優(yōu)勢在于適合高密度、細(xì)間距的封裝要求,可實(shí)現(xiàn)批量自動化生產(chǎn),具有優(yōu)異的電氣性能和散熱性能。然而,其前期投資大(需要定制化光刻掩模和專用設(shè)備)、工藝要求高(對準(zhǔn)精度要求嚴(yán)格)、受材料熱膨脹系數(shù)失配影響較大導(dǎo)致可靠性風(fēng)險(xiǎn)、且維修困難。因此,TAB技術(shù)主要應(yīng)用在大批量生產(chǎn)的特定產(chǎn)品上,如LCD驅(qū)動器等高密度引線連接場合。
五、混合鍵合:三維集成的未來趨勢
混合鍵合(Hybrid Bonding)是一種新型的三維集成封裝技術(shù),通過同時實(shí)現(xiàn)金屬鍵合(Cu-Cu)和介質(zhì)鍵合(氧化物-氧化物),在晶圓或芯片級別直接進(jìn)行物理和電氣連接。該技術(shù)無需傳統(tǒng)的銅柱或錫球等凸點(diǎn)結(jié)構(gòu),可實(shí)現(xiàn)超細(xì)互連間距(<1μm)的連接,互連密度極高。
混合鍵合的工藝流程包括鍵合前預(yù)處理、兩片晶圓預(yù)對準(zhǔn)鍵合和鍵合后熱退火處理三個關(guān)鍵步驟。首先,對晶圓進(jìn)行化學(xué)機(jī)械拋光/平坦化(CMP)和表面活化及清洗處理;然后,在室溫下將兩片晶圓緊密貼合,通過介質(zhì)SiO?上的懸掛鍵實(shí)現(xiàn)橋連;最后,通過熱退火處理促進(jìn)晶圓間介質(zhì)SiO?反應(yīng)和金屬Cu的互擴(kuò)散,形成永久鍵合。
混合鍵合的優(yōu)勢在于互連密度極高、鍵合界面平整度好、可實(shí)現(xiàn)更薄的晶圓堆疊,有利于三維集成。然而,其工藝難點(diǎn)主要在于光滑度、清潔度和對準(zhǔn)精度。目前,混合鍵合技術(shù)仍處于研發(fā)和產(chǎn)業(yè)化初期,但已被視為未來三維集成封裝的關(guān)鍵技術(shù)之一。
六、技術(shù)對比與應(yīng)用場景
四種鍵合方式在工藝特點(diǎn)、技術(shù)參數(shù)和應(yīng)用場景上存在顯著差異:
鍵合方式 | 工藝特點(diǎn) | 優(yōu)勢 | 劣勢 | 應(yīng)用場景 |
引線鍵合 | 細(xì)金屬引線連接 | 工藝成熟、成本低、靈活性好 | 封裝尺寸大、電氣性能受限 | |
倒裝芯片 | 凸點(diǎn)直接連接 | 互連密度高、散熱性能好 | 工藝復(fù)雜、成本高 | 高性能計(jì)算、移動通信 |
載帶自動鍵合 | 柔性載帶連接 | 自動化程度高、電氣性能優(yōu)異 | 前期投資大、維修困難 | LCD驅(qū)動器、高密度引線連接 |
混合鍵合 | 三維直接連接 | 互連密度極高、鍵合界面平整 | 工藝難度大、成本高 | 三維集成、異構(gòu)集成 |
七、未來展望
隨著芯片集成度的不斷提升和電子產(chǎn)品小型化趨勢的加劇,芯片封裝技術(shù)正朝著高密度、高性能、低成本的方向發(fā)展。四種鍵合方式各有優(yōu)劣,未來可能呈現(xiàn)以下趨勢:
- 技術(shù)融合:不同鍵合方式可能在特定應(yīng)用場景中實(shí)現(xiàn)融合,如引線鍵合與倒裝芯片的結(jié)合,或TAB技術(shù)與混合鍵合的互補(bǔ)。
- 工藝創(chuàng)新:新材料、新工藝和新設(shè)備的引入將推動鍵合技術(shù)的持續(xù)創(chuàng)新,如銅線鍵合替代金線鍵合、激光鍵合技術(shù)等。
- 三維集成:混合鍵合技術(shù)有望在三維集成封裝領(lǐng)域取得突破,推動芯片性能的進(jìn)一步提升。
- 智能制造:自動化、智能化和數(shù)字化技術(shù)的應(yīng)用將提高鍵合工藝的精度和效率,降低生產(chǎn)成本。
八、結(jié)論
芯片封裝中的四種鍵合方式各具特色,共同推動著芯片封裝技術(shù)的演進(jìn)。引線鍵合以其成熟度和低成本優(yōu)勢占據(jù)主導(dǎo)地位;倒裝芯片在高性能計(jì)算和移動通信領(lǐng)域展現(xiàn)出強(qiáng)大競爭力;載帶自動鍵合為高密度引線連接提供了自動化解決方案;混合鍵合則代表了三維集成的未來趨勢。未來,隨著技術(shù)的不斷創(chuàng)新和應(yīng)用場景的拓展,四種鍵合方式將繼續(xù)在芯片封裝領(lǐng)域發(fā)揮重要作用,共同推動半導(dǎo)體產(chǎn)業(yè)的持續(xù)發(fā)展。
-
芯片封裝
+關(guān)注
關(guān)注
11文章
576瀏覽量
31347 -
半導(dǎo)體設(shè)備
+關(guān)注
關(guān)注
4文章
395瀏覽量
15922
發(fā)布評論請先 登錄
PADS封裝中的四種庫
優(yōu)化封裝之鍵合線封裝中的兩個主要不連續(xù)區(qū)
先進(jìn)封裝技術(shù)的發(fā)展趨勢
無線充電技術(shù)的四種方式及其原理和應(yīng)用介紹
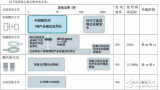
無線充電技術(shù)(四種主要方式)原理與應(yīng)用實(shí)例圖文詳解.
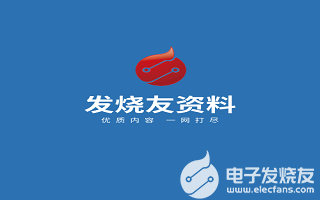
SiP封裝、合封芯片和芯片合封是一種技術(shù)嗎?都是合封芯片技術(shù)
芯片封裝鍵合技術(shù)工藝流程以及優(yōu)缺點(diǎn)介紹
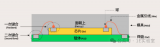
芯片封裝的四種鍵合技術(shù)
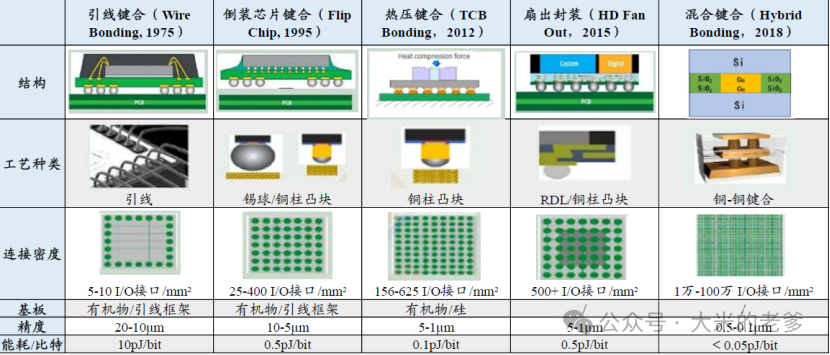
評論