摘要:碳化硅襯底切割對(duì)起始位置精度與厚度均勻性要求極高,自動(dòng)對(duì)刀技術(shù)作為關(guān)鍵技術(shù)手段,能夠有效提升切割起始位置精度,進(jìn)而優(yōu)化厚度均勻性。本文深入探討自動(dòng)對(duì)刀技術(shù)的作用機(jī)制、實(shí)現(xiàn)方式及其對(duì)切割工藝優(yōu)化的重要意義。
一、引言
碳化硅襯底是第三代半導(dǎo)體器件的核心基礎(chǔ)材料,其切割質(zhì)量直接影響器件性能與成品率。在碳化硅襯底切割過程中,起始位置精度不足會(huì)導(dǎo)致切割路徑偏移,造成材料浪費(fèi)與加工誤差;而厚度不均勻則會(huì)影響后續(xù)芯片制造工藝的穩(wěn)定性。自動(dòng)對(duì)刀技術(shù)通過精確確定刀具與工件的相對(duì)位置,為提升切割起始位置精度與優(yōu)化厚度均勻性提供了有效途徑。
二、自動(dòng)對(duì)刀技術(shù)原理與分類
(一)技術(shù)原理
自動(dòng)對(duì)刀技術(shù)基于傳感器獲取刀具與工件表面的位置信息,通過數(shù)據(jù)處理與控制系統(tǒng)實(shí)現(xiàn)刀具位置的精確調(diào)整。其核心在于快速、準(zhǔn)確地感知刀具與工件的接觸狀態(tài),將物理接觸信號(hào)轉(zhuǎn)化為電信號(hào)或數(shù)字信號(hào),進(jìn)而驅(qū)動(dòng)執(zhí)行機(jī)構(gòu)完成對(duì)刀操作 。
(二)常見分類
常見的自動(dòng)對(duì)刀技術(shù)包括接觸式對(duì)刀與非接觸式對(duì)刀。接觸式對(duì)刀通過刀具與工件直接接觸,利用壓力傳感器、電感傳感器等檢測(cè)接觸瞬間,實(shí)現(xiàn)位置校準(zhǔn);非接觸式對(duì)刀則借助激光、紅外等光學(xué)手段,在不接觸工件的情況下測(cè)量刀具與工件的相對(duì)位置,具有對(duì)刀具和工件無損傷、測(cè)量速度快等優(yōu)勢(shì)。
三、自動(dòng)對(duì)刀技術(shù)對(duì)切割起始位置精度的提升
(一)消除系統(tǒng)誤差
機(jī)床在長(zhǎng)期使用過程中會(huì)產(chǎn)生機(jī)械磨損、熱變形等系統(tǒng)誤差,影響切割起始位置精度。自動(dòng)對(duì)刀技術(shù)能夠?qū)崟r(shí)檢測(cè)刀具位置,通過補(bǔ)償算法修正機(jī)床坐標(biāo)系與工件坐標(biāo)系之間的偏差,消除因機(jī)床誤差導(dǎo)致的起始位置偏移,確保刀具準(zhǔn)確落于預(yù)設(shè)切割起始點(diǎn)。
(二)提高重復(fù)定位精度
對(duì)于批量碳化硅襯底切割,自動(dòng)對(duì)刀技術(shù)可在每次切割前自動(dòng)校準(zhǔn)刀具位置,避免人工對(duì)刀的主觀性與誤差,顯著提高切割起始位置的重復(fù)定位精度。即使在長(zhǎng)時(shí)間連續(xù)加工過程中,也能保證每片襯底的切割起始位置一致性,為后續(xù)切割質(zhì)量穩(wěn)定奠定基礎(chǔ)。
四、基于起始位置精度提升的厚度均勻性優(yōu)化
(一)保證切割路徑準(zhǔn)確性
精確的起始位置確保了切割路徑嚴(yán)格按照預(yù)設(shè)軌跡進(jìn)行。在碳化硅襯底切割中,若起始位置存在偏差,切割過程中刀具受力不均,易導(dǎo)致切割深度變化,進(jìn)而造成厚度不均勻。自動(dòng)對(duì)刀技術(shù)使刀具從準(zhǔn)確位置開始切割,保證切割過程中各點(diǎn)切削深度一致,有效提升厚度均勻性。
(二)實(shí)時(shí)反饋與調(diào)整
自動(dòng)對(duì)刀系統(tǒng)可與切割過程監(jiān)測(cè)系統(tǒng)聯(lián)動(dòng),在切割過程中實(shí)時(shí)監(jiān)測(cè)刀具位置與切割參數(shù)。一旦檢測(cè)到厚度異常趨勢(shì),系統(tǒng)能夠快速反饋并調(diào)整刀具位置或切割參數(shù),及時(shí)糾正偏差,維持切割厚度的穩(wěn)定性,實(shí)現(xiàn)對(duì)厚度均勻性的動(dòng)態(tài)優(yōu)化。
五、自動(dòng)對(duì)刀技術(shù)的實(shí)現(xiàn)與應(yīng)用
(一)硬件系統(tǒng)搭建
自動(dòng)對(duì)刀技術(shù)的實(shí)現(xiàn)依賴于高精度傳感器、高性能控制器與穩(wěn)定的執(zhí)行機(jī)構(gòu)。選用分辨率高、響應(yīng)速度快的傳感器(如納米級(jí)精度激光位移傳感器)實(shí)時(shí)采集位置信息;采用運(yùn)算能力強(qiáng)的控制器進(jìn)行數(shù)據(jù)處理與算法執(zhí)行;搭配高精度伺服電機(jī)等執(zhí)行機(jī)構(gòu),確保刀具位置調(diào)整的準(zhǔn)確性與快速性。
(二)軟件算法優(yōu)化
開發(fā)專用的自動(dòng)對(duì)刀軟件算法,實(shí)現(xiàn)傳感器信號(hào)的濾波、處理與分析,以及對(duì)刀策略的智能化決策。結(jié)合機(jī)器學(xué)習(xí)算法,根據(jù)歷史對(duì)刀數(shù)據(jù)與切割結(jié)果,優(yōu)化對(duì)刀參數(shù)與補(bǔ)償算法,提高自動(dòng)對(duì)刀的精度與適應(yīng)性,使其更好地滿足碳化硅襯底切割工藝需求。
高通量晶圓測(cè)厚系統(tǒng)運(yùn)用第三代掃頻OCT技術(shù),精準(zhǔn)攻克晶圓/晶片厚度TTV重復(fù)精度不穩(wěn)定難題,重復(fù)精度達(dá)3nm以下。針對(duì)行業(yè)厚度測(cè)量結(jié)果不一致的痛點(diǎn),經(jīng)不同時(shí)段測(cè)量驗(yàn)證,保障再現(xiàn)精度可靠。?
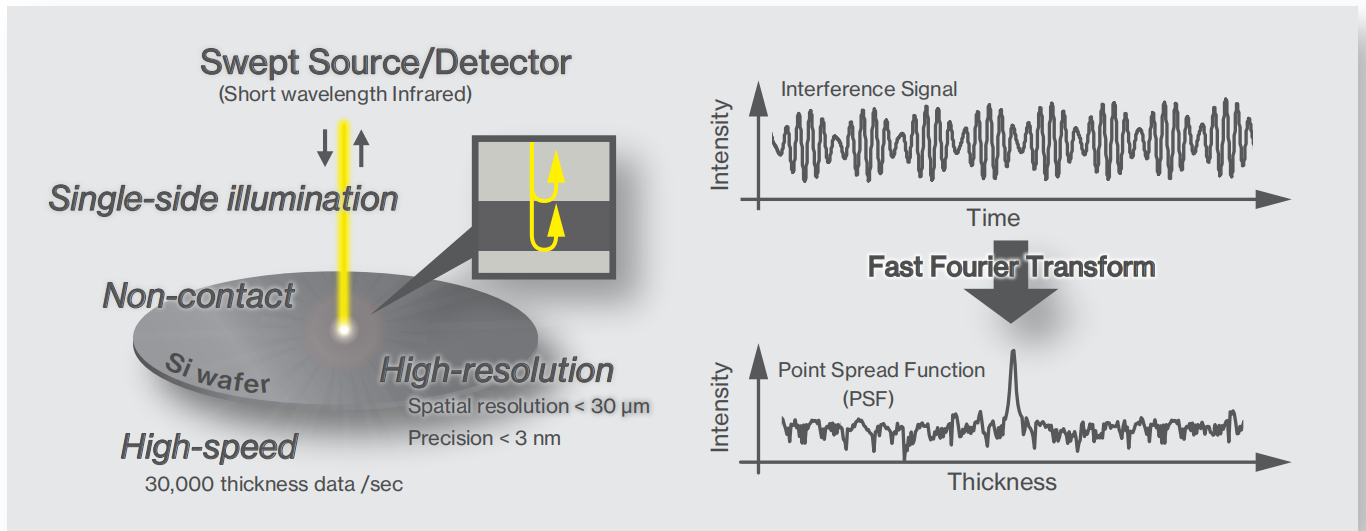
我們的數(shù)據(jù)和WAFERSIGHT2的數(shù)據(jù)測(cè)量對(duì)比,進(jìn)一步驗(yàn)證了真值的再現(xiàn)性:
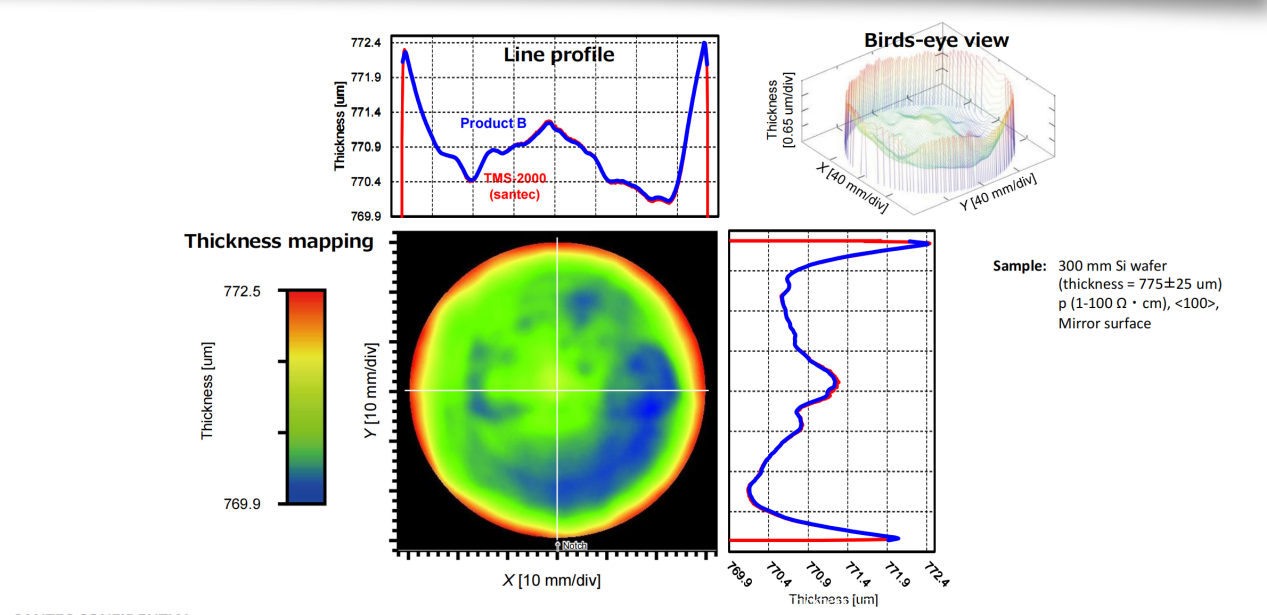
(以上為新啟航實(shí)測(cè)樣品數(shù)據(jù)結(jié)果)
該系統(tǒng)基于第三代可調(diào)諧掃頻激光技術(shù),相較傳統(tǒng)雙探頭對(duì)射掃描,可一次完成所有平面度及厚度參數(shù)測(cè)量。其創(chuàng)新掃描原理極大提升材料兼容性,從輕摻到重?fù)絇型硅,到碳化硅、藍(lán)寶石、玻璃等多種晶圓材料均適用:?
對(duì)重?fù)叫凸?,可精?zhǔn)探測(cè)強(qiáng)吸收晶圓前后表面;?
點(diǎn)掃描第三代掃頻激光技術(shù),有效抵御光譜串?dāng)_,勝任粗糙晶圓表面測(cè)量;?
通過偏振效應(yīng)補(bǔ)償,增強(qiáng)低反射碳化硅、鈮酸鋰晶圓測(cè)量信噪比;
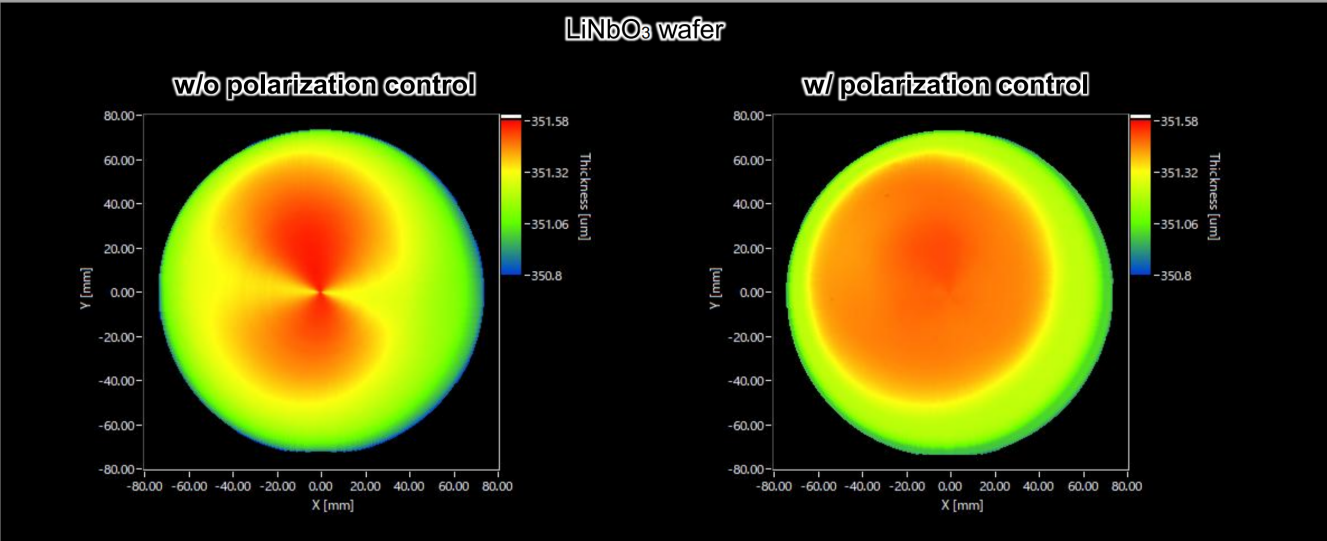
(以上為新啟航實(shí)測(cè)樣品數(shù)據(jù)結(jié)果)
支持絕緣體上硅和MEMS多層結(jié)構(gòu)測(cè)量,覆蓋μm級(jí)到數(shù)百μm級(jí)厚度范圍,還可測(cè)量薄至4μm、精度達(dá)1nm的薄膜。
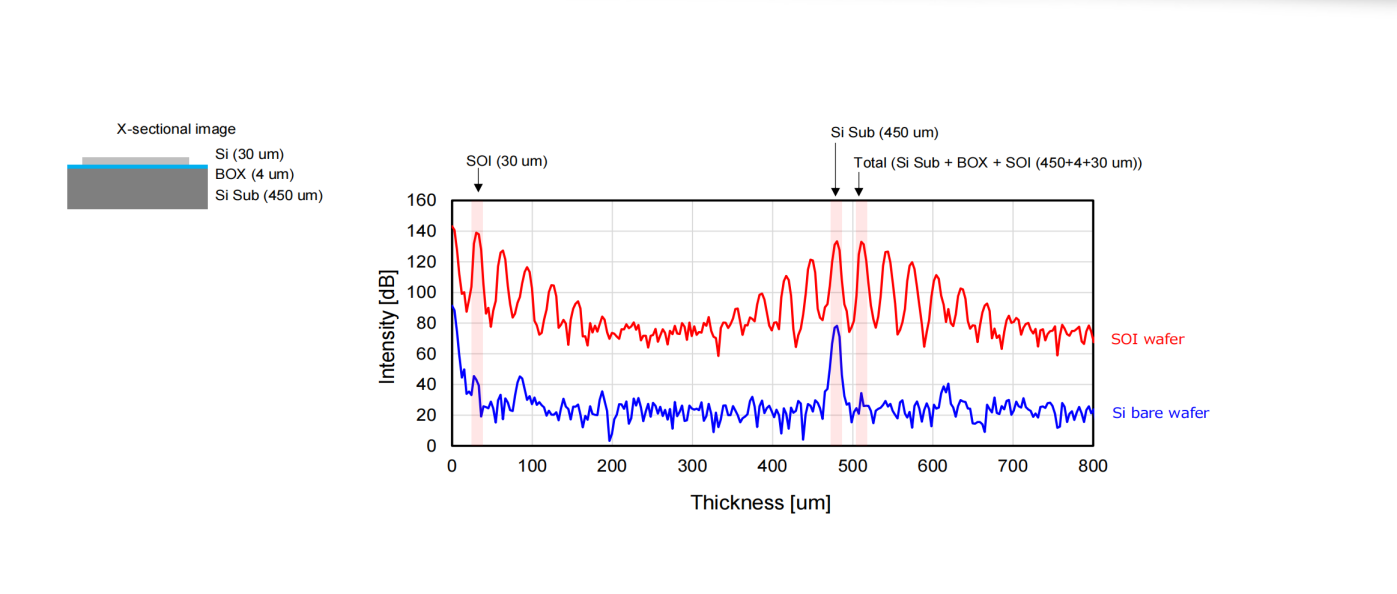
(以上為新啟航實(shí)測(cè)樣品數(shù)據(jù)結(jié)果)
此外,可調(diào)諧掃頻激光具備出色的“溫漂”處理能力,在極端環(huán)境中抗干擾性強(qiáng),顯著提升重復(fù)測(cè)量穩(wěn)定性。
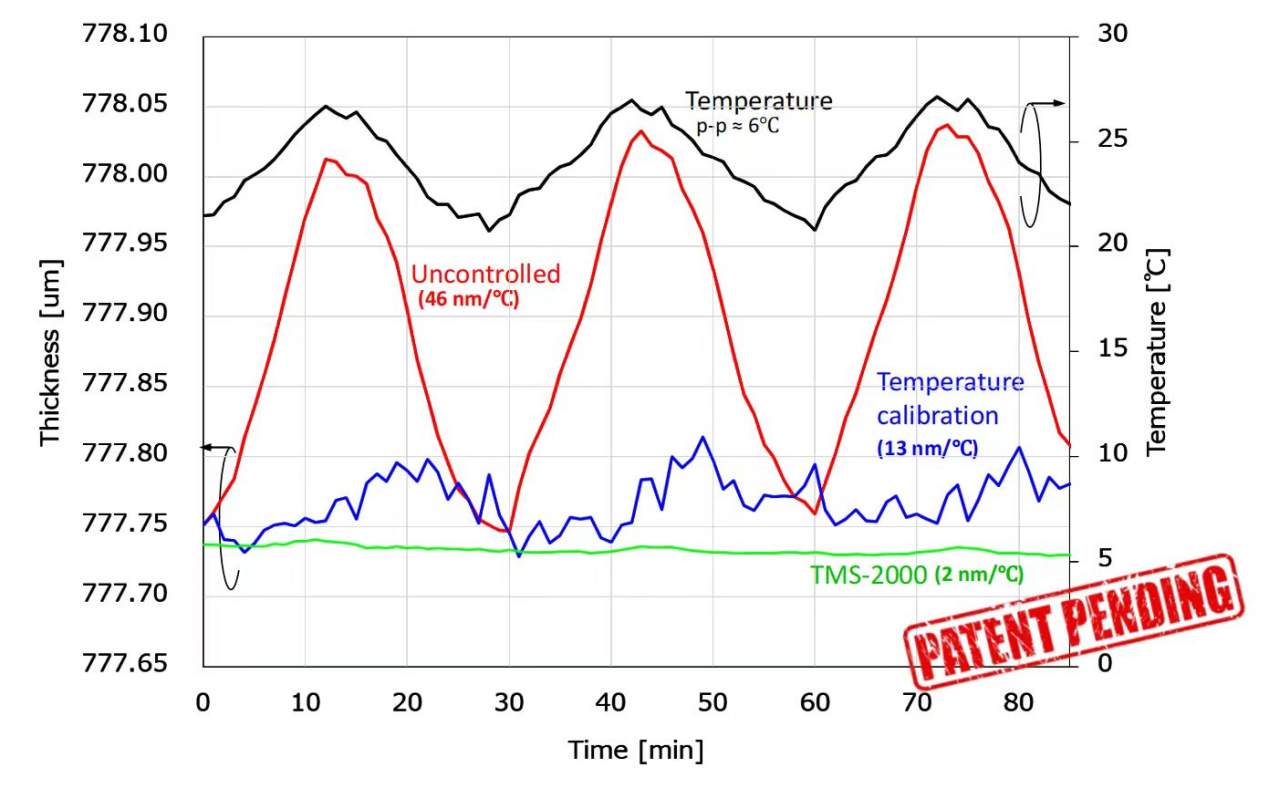
(以上為新啟航實(shí)測(cè)樣品數(shù)據(jù)結(jié)果)
系統(tǒng)采用第三代高速掃頻可調(diào)諧激光器,擺脫傳統(tǒng)SLD光源對(duì)“主動(dòng)式減震平臺(tái)”的依賴,憑借卓越抗干擾性實(shí)現(xiàn)小型化設(shè)計(jì),還能與EFEM系統(tǒng)集成,滿足產(chǎn)線自動(dòng)化測(cè)量需求。運(yùn)動(dòng)控制靈活,適配2-12英寸方片和圓片測(cè)量。
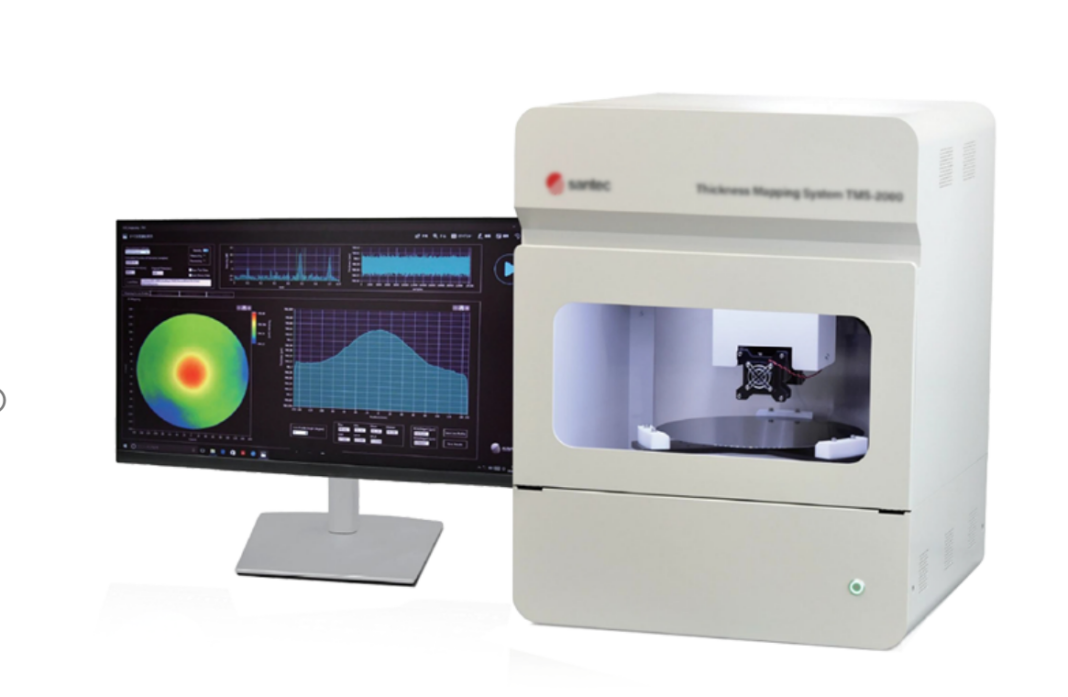
-
碳化硅
+關(guān)注
關(guān)注
25文章
3066瀏覽量
50468
發(fā)布評(píng)論請(qǐng)先 登錄
碳化硅的激光切割技術(shù)介紹
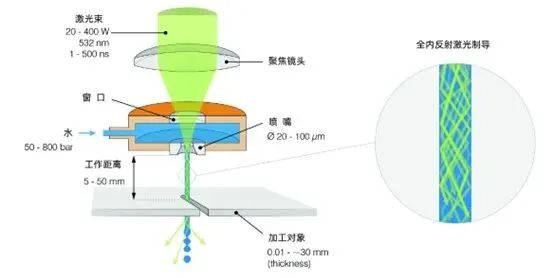
碳化硅深層的特性
碳化硅功率器件技術(shù)可靠性!
簡(jiǎn)述碳化硅襯底類型及應(yīng)用
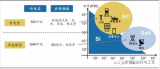
降低碳化硅襯底TTV的磨片加工方法
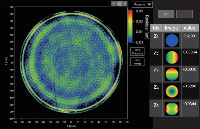
碳化硅襯底 TTV 厚度測(cè)量?jī)x器的選型指南與應(yīng)用場(chǎng)景分析
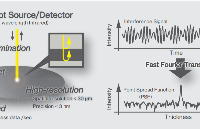
基于光纖傳感的碳化硅襯底厚度測(cè)量探頭溫漂抑制技術(shù)
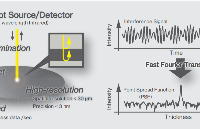
切割進(jìn)給量與碳化硅襯底厚度均勻性的量化關(guān)系及工藝優(yōu)化
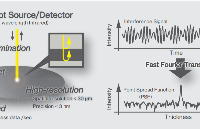
基于進(jìn)給量梯度調(diào)節(jié)的碳化硅襯底切割厚度均勻性提升技術(shù)
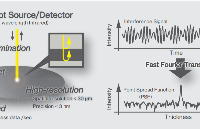
碳化硅襯底切割進(jìn)給量與磨粒磨損狀態(tài)的協(xié)同調(diào)控模型
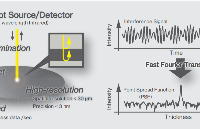
基于機(jī)器視覺的碳化硅襯底切割自動(dòng)對(duì)刀系統(tǒng)設(shè)計(jì)與厚度均勻性控制
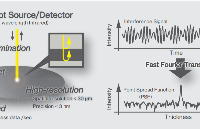
碳化硅襯底切割自動(dòng)對(duì)刀系統(tǒng)與進(jìn)給參數(shù)的協(xié)同優(yōu)化模型
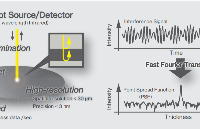
評(píng)論