文章來源:學(xué)習(xí)那些事
原文作者:前路漫漫
本主要講解了芯片封裝中銀燒結(jié)工藝的原理、優(yōu)勢、工程化應(yīng)用以及未來展望。
燒結(jié)工藝
燒結(jié)是將礦粉、熔劑與燃料按照精確的配比方案進(jìn)行調(diào)配,通過機(jī)械攪拌或氣流混合等方式實(shí)現(xiàn)均勻分散。在燃料劇烈燃燒營造的高溫環(huán)境中,部分原料發(fā)生熔化或軟化的物理變化,同時伴隨復(fù)雜的化學(xué)反應(yīng),諸如氧化物的還原、碳酸鹽的分解等。此過程中產(chǎn)生的液相物質(zhì)在溫度下降時逐漸凝固,通過顆粒間的黏結(jié)與再結(jié)晶,最終形成致密的塊狀物體。對于兩種不同金屬而言,它們能夠在遠(yuǎn)低于各自熔點(diǎn)的溫度區(qū)間,依據(jù)特定比例熔合形成共熔合金,這一臨界溫度被定義為低共熔點(diǎn),其數(shù)值取決于金屬成分的相互作用。
芯片封裝燒結(jié)
在芯片封裝領(lǐng)域,燒結(jié)工藝作為核心互連手段,具體實(shí)施時需在芯片與載體(包括基片或管殼)之間精準(zhǔn)置入合金焊料薄片。將組件置于真空腔室或充滿氮?dú)?、氬氣等保護(hù)氣體的環(huán)境中,通過梯度升溫至合金的共熔點(diǎn),促使焊料由固態(tài)轉(zhuǎn)變?yōu)橐簯B(tài)。液態(tài)合金憑借表面張力與浸潤特性,迅速鋪展覆蓋芯片襯底的焊接層金屬以及載體的焊接面,形成原子級別的緊密接觸。在此期間,焊料中的活性成分與金屬表面發(fā)生擴(kuò)散、溶解及化合反應(yīng),生成具有特定晶體結(jié)構(gòu)的金屬間化合物。當(dāng)溫度冷卻至共熔點(diǎn)以下,液態(tài)合金與金屬間化合物協(xié)同固化,在芯片與載體間構(gòu)建起低電阻的歐姆接觸,完成高性能的電氣互連。
銀燒結(jié)技術(shù)優(yōu)勢
銀燒結(jié)技術(shù),業(yè)界又稱低溫連接技術(shù),其性能優(yōu)勢體現(xiàn)在多個維度:首先,燒結(jié)形成的連接層以純銀為主,具備高達(dá) 63×10? S/m 的電導(dǎo)率與 429 W/(m?K) 的熱導(dǎo)率,可有效降低互連電阻與熱阻;其次,銀的 961℃高熔點(diǎn)使其在長期服役中,相較熔點(diǎn)低于 300℃的軟釬焊材料,能規(guī)避因溫度循環(huán)引發(fā)的疲勞裂紋擴(kuò)展,可靠性提升數(shù)倍;再者,燒結(jié)材料體系豐富,按銀顆粒物理形態(tài)可細(xì)分為觸變性銀漿、自支撐銀膜及流動性銀粉,按尺寸劃分為微米級(1-100μm)、納米級(1-100nm)及混合級(兼具微米骨架與納米活性);最后,銀的化學(xué)穩(wěn)定性賦予其卓越的抗硫化、抗電化學(xué)腐蝕能力,配合極低的蠕變速率,確保在高溫高濕環(huán)境下仍維持連接界面的完整性。
燒結(jié)原理示意圖
納米銀顆粒特性與應(yīng)用困境
納米級銀顆粒因量子尺寸效應(yīng),表面原子占比激增導(dǎo)致熔點(diǎn)顯著下降,部分納米銀的初始燒結(jié)溫度可低至 150℃。處于熔融態(tài)的納米顆粒通過液相毛細(xì)力驅(qū)動,發(fā)生頸縮、融合與 Ostwald 熟化過程,最終形成具有塊體銀強(qiáng)度的燒結(jié)體。然而,產(chǎn)業(yè)化應(yīng)用面臨雙重挑戰(zhàn):工藝層面,傳統(tǒng)熱壓燒結(jié)需施加 5-50 MPa 壓力,既限制自動化產(chǎn)線適配性,又存在芯片碎裂風(fēng)險;雖發(fā)展出無壓燒結(jié)與微波閃燒等新工藝,但 250-350℃的燒結(jié)溫度仍高于多數(shù)聚合物封裝材料的耐熱極限,無法替代 Sn-Pb 焊料的中溫工藝窗口。安全層面,納米銀顆粒(10?? m 量級)可穿透人體角質(zhì)層,經(jīng)皮膚吸收后可能富集于肝臟、腎臟等器官,目前缺乏完善的職業(yè)暴露防護(hù)標(biāo)準(zhǔn),制約了其大規(guī)模工業(yè)應(yīng)用。
銀燒結(jié)材料優(yōu)化與機(jī)制
為抑制微米 / 納米銀顆粒的團(tuán)聚傾向,常引入分散劑、黏結(jié)劑等有機(jī)添加劑構(gòu)建穩(wěn)定體系。在燒結(jié)過程中,有機(jī)物經(jīng)歷三個階段變化:低溫段(<150℃)溶劑揮發(fā),中溫段(150-300℃)高分子分解,高溫段(>300℃)殘余碳氧化,最終在連接層中僅留存純度>99.9% 的銀相。該技術(shù)的本質(zhì)是基于銀原子的體擴(kuò)散與表面擴(kuò)散機(jī)制:在溫度激活下,銀原子跨越顆粒界面遷移,通過晶格重組形成冶金結(jié)合。當(dāng)前研究聚焦納米銀漿的界面工程,通過表面修飾降低燒結(jié)活化能,以期實(shí)現(xiàn) 180℃以下的無壓互連,推動電子封裝向高集成、高可靠方向發(fā)展。
納米級銀顆粒的燒結(jié)歷程呈現(xiàn)出顯著的階段性特征。初始階段以顆粒間的物理接觸為起點(diǎn),在原子級尺度上,銀顆粒表面活性位點(diǎn)相互作用形成燒結(jié)頸。此階段主導(dǎo)原子遷移的表面擴(kuò)散機(jī)制,源于納米顆粒極高的比表面積——每單位質(zhì)量的顆粒暴露著海量表面原子,這些原子因配位不飽和而具備高化學(xué)活性,自發(fā)向接觸區(qū)域匯聚,促使燒結(jié)頸緩慢生長。隨著燒結(jié)進(jìn)程推進(jìn)至中間階段,原子遷移模式轉(zhuǎn)向體擴(kuò)散與晶界擴(kuò)散。銀原子跨越顆粒內(nèi)部晶格或沿晶界路徑,持續(xù)填充燒結(jié)頸區(qū)域。在此期間,顆粒間距以納米級精度逐步縮減,孤立的顆粒通過燒結(jié)頸的擴(kuò)展相互連接,構(gòu)建起三維貫通的孔隙網(wǎng)絡(luò)。該網(wǎng)絡(luò)結(jié)構(gòu)的演變直接關(guān)聯(lián)材料性能提升:隨著原子重排與鍵合增強(qiáng),燒結(jié)層密度從松散顆粒態(tài)向致密結(jié)構(gòu)過渡,其力學(xué)強(qiáng)度與導(dǎo)電導(dǎo)熱性能呈指數(shù)級增長。燒結(jié)后期聚焦于孔隙的精細(xì)化演變。原本連續(xù)的孔洞在表面張力驅(qū)動下發(fā)生球化,隨后通過 Ostwald 熟化機(jī)制逐步縮小。這一過程中,小孔洞因曲率驅(qū)動的原子蒸氣壓差異被逐漸消除,大孔洞則持續(xù)收縮。當(dāng)工藝參數(shù)匹配理想狀態(tài)時,最終形成接近理論密度的微觀結(jié)構(gòu),僅殘留亞微米級孤立孔隙。驅(qū)動這一復(fù)雜過程的能量源包含多重因素。表面能作為核心驅(qū)動力,與顆粒尺寸呈現(xiàn)反比關(guān)系——納米級銀顆粒因尺寸縮減至1-100 nm,其表面能密度可達(dá)塊體銀的數(shù)十倍,形成強(qiáng)大的熱力學(xué)驅(qū)動力。此外,外部施加的壓力、體系內(nèi)的化學(xué)勢梯度以及顆粒接觸產(chǎn)生的局部應(yīng)力場,均協(xié)同促進(jìn)原子的定向遷移。這些驅(qū)動力的疊加效應(yīng),在微觀層面決定著銀原子擴(kuò)散路徑與速率。
經(jīng)燒結(jié)形成的連接層展現(xiàn)出獨(dú)特的多孔結(jié)構(gòu)特性。盡管存在微米級孔隙網(wǎng)絡(luò),但其導(dǎo)電率仍能維持純銀的90%(孔隙率10%時),熱導(dǎo)率提升至軟釬焊材料的3倍,熱阻降至后者的1/15。這種性能優(yōu)勢在功率模塊應(yīng)用中轉(zhuǎn)化為顯著的壽命提升:銀燒結(jié)互連結(jié)構(gòu)的功率循環(huán)次數(shù)可達(dá)軟釬焊的2-3倍,同時層厚減少70%,有效緩解了傳統(tǒng)焊接工藝的熱阻瓶頸。然而,銀燒結(jié)工藝的工程化應(yīng)用面臨參數(shù)調(diào)控的復(fù)雜挑戰(zhàn)。傳統(tǒng)熱壓燒結(jié)需施加40 MPa壓力,該值已接近硅芯片材料的臨界承壓能力(53.6 MPa),極易在芯片表面形成應(yīng)力集中區(qū),引發(fā)裂紋或電學(xué)性能劣化。同時,壓力維持系統(tǒng)與自動化產(chǎn)線的兼容性較差,推動了無壓燒結(jié)技術(shù)的發(fā)展。無壓工藝雖犧牲部分致密度(孔隙率略增),但憑借銀原子的自擴(kuò)散特性,仍能實(shí)現(xiàn)優(yōu)異的導(dǎo)電可靠性,尤其適用于小尺寸芯片與低功率密度封裝場景。
溫度參數(shù)對燒結(jié)質(zhì)量的非線性影響
溫度參數(shù)對燒結(jié)質(zhì)量的影響呈現(xiàn)非線性特征。銀漿料中的有機(jī)添加劑需經(jīng)歷分階段分解:100℃以下完成溶劑揮發(fā),200-300℃區(qū)間發(fā)生高分子鏈的氧化裂解。只有當(dāng)有機(jī)物完全脫除后,銀顆粒方能建立直接冶金接觸。研究表明,在恒定壓力下,200-280℃溫度區(qū)間內(nèi)剪切強(qiáng)度隨溫度上升顯著提高,超過該范圍后增幅趨緩。值得注意的是,不同粒徑的銀顆粒(納米級 vs 微米級)對應(yīng)不同的最佳溫度窗口,需通過工藝設(shè)計精確匹配。
時間維度下的燒結(jié)動力學(xué)特征
時間維度上,燒結(jié)動力學(xué)曲線呈現(xiàn)典型的“S”型特征。初期幾秒至數(shù)十秒內(nèi),顆??焖偃诤闲纬煞€(wěn)定骨架,剪切強(qiáng)度實(shí)現(xiàn)80%以上的增長;后續(xù)延長時間雖可繼續(xù)提升致密度,但邊際效益遞減。這種動力學(xué)特性要求工程師在可靠性與生產(chǎn)效率間尋求平衡——過度延長燒結(jié)時間不僅增加能耗,還可能引發(fā)界面金屬間化合物的過度生長。
表面工程在銀燒結(jié)中扮演關(guān)鍵角色。為抑制銅基底的高溫氧化,常采用“鎳阻擋層+貴金屬鍍層”的復(fù)合結(jié)構(gòu):底層鎳層(厚度0.5-2 μm)通過擴(kuò)散屏障效應(yīng)延緩銅原子遷移,頂層銀或金鍍層(0.1-1 μm)為銀漿提供高活性燒結(jié)界面。鍍層粗糙度需與銀顆粒尺寸精密匹配:當(dāng)粗糙度Ra值控制在銀顆粒平均粒徑的1/3-1/2時,可實(shí)現(xiàn)最佳浸潤效果與機(jī)械嵌合。這種多尺度界面優(yōu)化策略,成為突破銀燒結(jié)工藝瓶頸的核心技術(shù)路徑。
銀燒結(jié)與軟釬焊的環(huán)境工藝對比
銀燒結(jié)工藝與軟釬焊的真空回流焊在環(huán)境選擇上存在本質(zhì)差異。常規(guī)銀燒結(jié)作業(yè)通常以空氣為介質(zhì),這一設(shè)定源于銀漿內(nèi)部有機(jī)成分的特性——在燒結(jié)進(jìn)程中,需借助氧氣參與氧化反應(yīng),促使有機(jī)物質(zhì)燒蝕分解,故而對環(huán)境中的氧含量存在硬性需求。而當(dāng)銀燒結(jié)工藝引入真空回流焊模式時,則依托真空燒結(jié)爐構(gòu)建精密可控的氣氛環(huán)境,通過有序執(zhí)行預(yù)熱、排氣、深度抽真空、梯度升溫、緩速降溫及保護(hù)性進(jìn)氣等操作環(huán)節(jié),配合定制化的溫度曲線與氣體流量控制策略,實(shí)現(xiàn)對燒結(jié)全過程的精準(zhǔn)調(diào)控。
真空燒結(jié)優(yōu)勢
相較于傳統(tǒng)焊接工藝,真空燒結(jié)技術(shù)展現(xiàn)出三重顯著優(yōu)勢:其一,因完全摒棄助焊劑的使用,徹底規(guī)避了助焊劑殘留引發(fā)的清潔工序及潛在腐蝕風(fēng)險;其二,通過抽真空手段將爐內(nèi)氧含量降至極低水平,從根源上抑制金屬氧化物的生成,保障焊接界面的純凈度;其三,真空環(huán)境下,焊料內(nèi)部及界面吸附的氣體在燒結(jié)完成前即沿邊緣充分逸散,確保焊接面呈現(xiàn)無氣泡的致密狀態(tài)。對比非真空加壓燒結(jié)工藝,二者核心分歧聚焦于焊料形態(tài):非真空工藝依賴含豐富有機(jī)載體的銀漿體系,需經(jīng)高溫氧化燒蝕完成有機(jī)物脫除;而真空工藝多采用預(yù)制焊片,其成分以金屬合金為主,無有機(jī)物揮發(fā)需求,從而簡化工藝路徑。
燒結(jié)焊料選取的一般原則
銀燒結(jié)工藝的工程化應(yīng)用
燒結(jié)焊料的選型需緊密貼合應(yīng)用場景特性。含銀基焊料憑借相似金屬界面的浸潤優(yōu)勢,與鍍銀端面展現(xiàn)出良好的接合匹配性;含金、銦元素的合金焊料則對鍍金表面具備更強(qiáng)的親和能力;金錫合金因固有硬度高、延展性差(延伸率低)的特性,在大面積芯片焊接中易引發(fā)應(yīng)力集中,適用性受限;針對背面材質(zhì)為硅(Si)的芯片,優(yōu)選鍍金基片作為載體,并對鍍層厚度提出量化要求(通常需≥X μm),在此場景下,金銻、金硅系焊料因熱膨脹系數(shù)匹配度高、界面反應(yīng)可控,成為工藝首選。不同焊料的適配準(zhǔn)則詳見表3-2所歸納的材質(zhì)-應(yīng)用對應(yīng)關(guān)系矩陣。
在銀燒結(jié)工藝實(shí)踐中,工藝參數(shù)與材料狀態(tài)對成品性能存在顯著影響。統(tǒng)計數(shù)據(jù)顯示,芯片面積每增加10%或燒結(jié)層厚度提升5μm,剪切強(qiáng)度平均下降8%-12%,該現(xiàn)象歸因于應(yīng)力分布不均與擴(kuò)散路徑延長。此外,基片、載體、焊料及芯片背面的污染(如油脂、塵埃殘留)會形成擴(kuò)散屏障,阻礙合金原子的跨界面遷移,導(dǎo)致燒結(jié)界面結(jié)合力下降。長期存放的材料(超過30天)因表面氧化層增厚(氧化物厚度>50nm),即便經(jīng)預(yù)處理,殘留氧化膜仍會在焊料熔融后形成微米級空洞,降低連接層致密度。在此情境下,向爐腔引入體積分?jǐn)?shù)0.5%-2%的氫氣,可通過H?+MeO→H?O+Me反應(yīng)還原部分金屬氧化物,改善界面純凈度。
工藝實(shí)施層面,壓力調(diào)控是關(guān)鍵環(huán)節(jié)。在芯片表面施加1-5MPa壓力可使界面間隙從20μm縮減至5μm以下,顯著減少空洞形成。但直接施壓易造成芯片表面劃痕或裂紋(損傷概率隨壓力超2MPa呈指數(shù)上升),工程中普遍采用等面積保護(hù)硅片(厚度0.2-0.5mm)作為緩沖層,既傳遞壓力又避免直接接觸損傷。鑒于燒結(jié)過程中氣流擾動(如真空切換或氣體吹掃)可能導(dǎo)致芯片偏移(位移量>100μm時焊接失效),需使用高精度夾具定位。高純石墨夾具(純度>99.95%)因具備150W/(m·K)導(dǎo)熱率、1500℃熱穩(wěn)定性及0.5%熱膨脹系數(shù),能在維持溫度均勻性的同時提供可靠夾持力。
燒結(jié)流程遵循“預(yù)熱-保溫-冷卻”三段式曲線:預(yù)熱階段以5-10℃/min速率升至焊料共晶點(diǎn)以下50℃,消除濕氣與應(yīng)力;保溫階段維持高于共晶點(diǎn)30-50℃(典型值如銀基焊料280-320℃),持續(xù)10-30min確保充分?jǐn)U散;冷卻階段以8-12℃/min降至室溫。需強(qiáng)調(diào)的是,銀燒結(jié)并非簡單共晶過程,其微觀組織由Ag?Sn、Ag-Cu固溶體等多種金屬間化合物交織而成,經(jīng)再結(jié)晶形成蜂窩狀致密結(jié)構(gòu),較傳統(tǒng)釬焊多出晶界強(qiáng)化與固溶強(qiáng)化機(jī)制。
質(zhì)量檢測方面,因銀燒結(jié)層空洞尺寸集中于0.5-5μm,常規(guī)X光(分辨率>10μm)與超聲掃描(盲區(qū)>2μm)難以識別。目前依賴芯片推剪試驗(yàn)(剪切速率0.5mm/min)量化結(jié)合力,實(shí)測數(shù)據(jù)顯示,銀燒結(jié)層抗剪強(qiáng)度可達(dá)80-120MPa,遠(yuǎn)超芯片(硅基材料抗剪強(qiáng)度30-50MPa),導(dǎo)致90%以上失效模式表現(xiàn)為芯片本體碎裂而非焊層脫粘。
可靠性評估聚焦熱應(yīng)力管理。由于硅(CTE 2.6ppm/℃)與銀(CTE 18ppm/℃)的膨脹系數(shù)差異,在-40℃至150℃循環(huán)測試中,界面熱應(yīng)力可達(dá)50-80MPa。與具備10%-20%蠕變應(yīng)變能力的軟釬焊料不同,銀燒結(jié)層(蠕變率<0.1%)缺乏應(yīng)力緩沖,需通過材料匹配降低風(fēng)險。工程實(shí)踐表明,采用CTE介于5-8ppm/℃的中間層材料(如鎢銅合金),配合仿真優(yōu)化芯片-焊層-基板的疊層結(jié)構(gòu),可將熱應(yīng)力峰值降低40%以上。
而燒結(jié)銀的強(qiáng)度較大但比較薄,不像軟釬焊料也可以有一定的蠕性形變,能吸收應(yīng)力,從而使得上下表面的應(yīng)力差值不那么大,而減少對芯片的損害,所以燒結(jié)銀對材料強(qiáng)度相對較小的硅基芯片,在使用這種工藝時要綜合考慮材料的CT匹配,從選材到結(jié)構(gòu)上綜合考量,先做仿真應(yīng)力計算,優(yōu)選材料,包括塑封料?;诖算y燒結(jié)工藝與第三代寬禁帶半導(dǎo)體形成天然適配。以SiC功率模塊為例,其200℃以上工作結(jié)溫遠(yuǎn)超硅基器件(175℃上限),而銀燒結(jié)層961℃熔點(diǎn)可確保長期高溫穩(wěn)定性。實(shí)測數(shù)據(jù)顯示,SiC模塊經(jīng)銀燒結(jié)封裝后,功率密度提升3倍,熱阻降低60%,在電動汽車OBC、光伏逆變器等場景展現(xiàn)出替代傳統(tǒng)焊接的潛力。此外,無鉛銀基材料符合RoHS標(biāo)準(zhǔn),其250-350℃燒結(jié)溫度與現(xiàn)有回流焊設(shè)備兼容,進(jìn)一步加速了產(chǎn)業(yè)應(yīng)用進(jìn)程。
未來展望
回溯技術(shù)演進(jìn)軌跡,銀及金屬燒結(jié)工藝早期憑借超高焊接強(qiáng)度與穩(wěn)定性,深度嵌入軍用電子高可靠封裝體系。伴隨新能源汽車功率模塊需求爆發(fā),銀燒結(jié)技術(shù)以顛覆性優(yōu)勢脫穎而出:其構(gòu)建的互連層導(dǎo)電率達(dá)63 MS/m,熱導(dǎo)率突破420 W/(m·K),相較傳統(tǒng)釬焊實(shí)現(xiàn)熱阻降低80%、功率密度提升3倍。盡管當(dāng)前工藝已步入產(chǎn)業(yè)化成熟期,設(shè)備端真空熱壓系統(tǒng)單臺成本超200萬元,材料側(cè)納米銀漿單價達(dá)3000元/克,較Sn-Pb焊料溢價超20倍。但技術(shù)革新正重塑成本曲線:國內(nèi)團(tuán)隊開發(fā)的微波閃燒結(jié)設(shè)備將能耗降低60%,納米銀粉水相合成法使原料成本下降40%。
在第三代半導(dǎo)體革命浪潮中,SiC器件200℃+的結(jié)溫工況與銀燒結(jié)層961℃熔點(diǎn)形成天然適配。
面向未來,封裝技術(shù)的競爭焦點(diǎn)已從單一材料性能轉(zhuǎn)向系統(tǒng)級協(xié)同優(yōu)化。研究顯示,通過梯度熱膨脹系數(shù)設(shè)計——在芯片與基板間引入鎢銅緩沖層,可使界面熱應(yīng)力降低72%。這種跨尺度材料工程思維,預(yù)示著封裝創(chuàng)新將邁向"性能-成本-可靠性"三維平衡的新階段。當(dāng)銀燒結(jié)工藝突破設(shè)備國產(chǎn)化與材料規(guī)模化瓶頸,其有望重構(gòu)功率半導(dǎo)體封裝的產(chǎn)業(yè)版圖。
-
工藝
+關(guān)注
關(guān)注
4文章
657瀏覽量
29170 -
焊接
+關(guān)注
關(guān)注
38文章
3371瀏覽量
60771 -
芯片封裝
+關(guān)注
關(guān)注
11文章
562瀏覽量
31155
原文標(biāo)題:銀燒結(jié)
文章出處:【微信號:bdtdsj,微信公眾號:中科院半導(dǎo)體所】歡迎添加關(guān)注!文章轉(zhuǎn)載請注明出處。
發(fā)布評論請先 登錄
相關(guān)推薦
低溫?zé)o壓燒結(jié)銀在射頻通訊上的5大應(yīng)用,除此之外,燒結(jié)銀還有哪些應(yīng)用呢?歡迎補(bǔ)充
150℃無壓燒結(jié)銀最簡單三個步驟
芯片封裝測試流程詳解ppt
到底什么電子燒結(jié)?
LED燈珠的生產(chǎn)工藝及封裝工藝
IC封裝工藝測試流程的詳細(xì)資料詳解
半燒結(jié)型銀漿粘接工藝在晶圓封裝的應(yīng)用
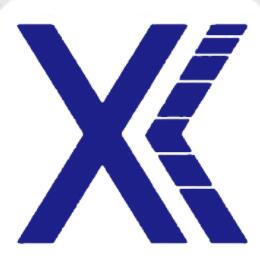
晶圓級封裝用半燒結(jié)型銀漿粘接工藝
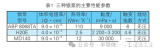
基于低溫焊料的真空燒結(jié)工藝研究
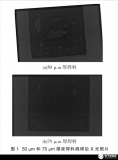
碳化硅SiC芯片封裝:銀燒結(jié)與銅燒結(jié)設(shè)備的技術(shù)探秘
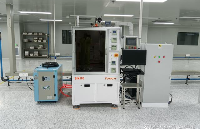
評論